精益管理:手、脑、心法的使用,逐步推进才能真正落地!
- 2021-12-27 14:08:00
- 周洪涛 转贴
- 647
于是全世界掀起一股学习、引进精益生产之风,可谓轰轰烈烈。可是,30年过去了,真正的成功者依然寥寥,这是为什么呢? 原因在于,精益生产管理体系推行有几个瓶颈关隘层次,突破不了,只能一直在原来层次徘徊。

如同企业经营,所有企业家都知道,经营业绩1000万向1个亿突破很难,多少年都会徘徊在3000~5000万; 1个亿向10个亿突破很难,多少年都只能在3~5亿徘徊,这些都是遇到了发展的底层瓶颈,需要用心突破底层逻辑才行。
很多推行精益生产的企业,推行多少年,还一直只停留在原来层次,他们以为这样就是精益生产了。
实际上,即使长久坚持,也只是维持,没有进步。 推行精益生产必须实现螺旋式上升,且有三个层次,首先是洗手层次,其次是洗脑层次,最后是洗心层次。
一、洗手层次
洗手,意味着已经在干活,尤其是精益生产比较推崇的在一线现场改善,活干多了,手自然会脏,洗洗手势必会成为这个阶段的必然。
一项变革推行起来一定会很困难,在小范围,选几个有创新意识的员工,做出一些改善示范和标杆是一些咨询公司推进精益生产常用的手段和途径, 从易到难,从局部到整体,从现场到后台,动手这是任何管理变革第一要干的事情。
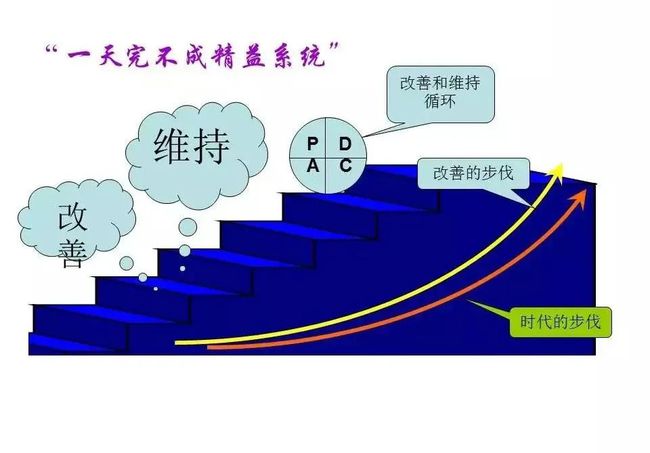
“5S”:整理(SEIRI)、整顿(SEITON)、清扫(SEISO)、清洁(SEIKETSU)、素养(SHITSUKE)五方面工作,因均以“S”开头,简称5S。
实际上大家刚开始做的还只是4S,整理、整顿、清扫、清洁,还远远谈不上素养。素养是一种习惯,是一种无意识的行动和意识,那可是一辈子的事情,没有3~5年时间根本不用谈素养。
当然4S是一项最需要动手的工作,清理现场经年累月积攒下来的各种物资,区别分类;把现场所有设备、物料、物品等定置定位,需要摆弄和挪位;最后用笤帚、毛巾、水、拖把进行擦拭和清洁工作。
所以现场常常是一双双脏手,这代表精益生产这项工作已经开始上路了。
业界以为,5S工作是精益生产入门的门槛,如同一屋不扫,何以扫天下一样,5S搞不好,何以搞单件流,何以提升生产效益效率,何以搞精益生产?
起初动手干的整体还属于技术、工具、技巧阶段,属于战术阶层,使用的多是精益工具,例如5S、看板、换模、节拍、价值流等等,全是手法。
这一层次基本上由咨询顾问主导,企业跟随学习为主。目前社会上推行精益生产的芸芸众企,99%都停留在这个阶段。
二、洗脑层次
很多事情,等到万事俱备时才去做,已经不是这个时代的规则了。
当条件只具备60%时,只要大致方向正确,就要去干,在过程中去解决困难,去创造条件,不能一味强调前提。不确定性也是一种工作之美,边干边想,回头再想。
但是长期只顾埋头干,不静下心来想象这件事情的来龙去脉,那是一种蛮干,迟早要出事的。
推行精益生产工作也一样,经历过“动手”阶段以后,必须要从管理思想、管理体系上进行深刻学习、理解、消化和创新,形成切合自身企业特点的精益生产管理体系。
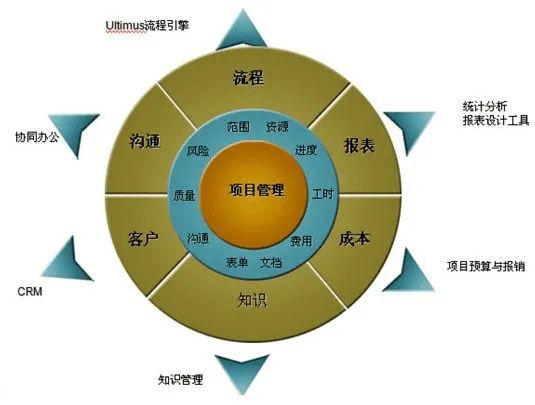
一是工业1.0,1861年蒸汽机的发明应用使手工业向机器大工业生产制造转变,实现第一次工业革命;
二是工业2.0,1910年以泰勒的科学管理和福特大量制造模式为代表,形成第二次工业革命;
三是工业3.0,1990年随着《改变世界的机器》的出版,丰田的准时化、自动化生产即丰田生产模式浮出水面,精益生产方式成为工业3.0的标志。
丰田生产方式看起来像是一些理应容易掌握的经营活动的工具和原则的简单集合,但是学习丰田20年、30年之后,除了丰田依然基业长青,我们还没有发现世界上任何一个公司能够像丰田汽车那样---系统、高效和持续地提升质量和成本优势,为什么,这其中魔力何在?
- 你知道他们产品标准化和模块化是怎么做的吗?
- 你知道他们供应链是如何管理的吗?
- 你知道他们MES系统中的逻辑是怎么设定的吗?
- 你知道他们产销计划是怎么做的吗?
- 你知道他们TPM和换模是怎么做的吗?
- 你知道他们公司领导力和企业文化是怎么做的吗?
这才是丰田精益生产的真经。
我们必须从底层逻辑弄懂、弄通,没有理解丰田背后潜在的逻辑,简单的复制丰田的方法可能并不起作用,也不能产生持续改进的效果。
动脑思考属于方向、体系阶段,属于战略阶层,应用的多是流程体系。
例如研发流程IPD,供应链体系ISC,VSM价值流程,拉动生产体系,改善建议制度,5个为什么问题溯源制度以及TPM设备保养制度等,全是流程体系,必须花脑筋去理解和揣摩,实现理论、思想层次的突破。
这一层次基本上由企业历经“洗手”阶段的精益骨干和高管主导。
目前社会上推行精益生产的企业,只有0.99%的企业能达到这个层次,算是百里挑一。代表企业主要有本田、松下、福特、通用、大众、富士康、伟创力、海尔等。
三、洗心层次
有幸能到丰田工厂亲身体验的人很幸运,但我们能学到什么呢?
去开开眼界可以,妄想能够学到丰田的看家本领,那是绝对不可能的。
几十年了,世界各地的企业领导者参观后学到了吗,怎么丰田还依然是精益生产的鼻祖,为什么,因为我们学不到他们存在于空气中的东西!
例如5S,它不仅仅是“打扫卫生”,它是一种管理方法论;更体现出全体员工的精、气、神,客户看重的不是表面的干净,而是这个企业的一种精神,一种文化,一种做事的态度。
看似简单的5S,中国有几家企业能够十年如一日认真做下来的,背后全是管理心法!这些丰田是不会告诉你,因为这才是丰田精益生产的真经。
这个层次就需要文化上场了,正如丰田所强调的:丰田模式重心在于文化---员工的思考和行为方式深深地植根于公司的理念和原则,其核心是对员工的尊重和持续改善,并始终坚持。
1981年,韦尔奇接任第八任通用电气公司总裁,力推“群策群力”的企业文化,终于把公司重新带上了发展的快车道。
从此,在他带领下的GE创造了一串串令人啧啧称奇的业绩,最后到2000年一跃成为全球最强大的公司。
本田的“Waigaya”文化。在Waigaya的讨论中,没有愚蠢的问题,没有标准答案,没有身份和等级限制,只有思想碰撞和创新创意。
本田的Waigaya文化创造出“三快”主义:研发和生产快乐地创、制造、市场和代理商快乐地销售、顾客快乐地购买。本田作为世界500强,有14万名员工,历史上本田从未亏损过。
李锦记的“爽”文化,公司有一套“爽指数”评估体系,用于衡量员工某一个时间段在健康、家庭和事业等方面的综合感受。
员工不爽,任何工作也做不好;员工爽了,才会快乐工作,热爱自己的工作,积极主动地为公司的发展贡献自己的创意和价值。
管理学上有一个著名的霍桑实验,这个实验表明:决定一个人工作的积极性和工作效率的最重要因素,不是薪水、职位、工作条件等外界因素,而是被他人认可、被尊重、成就感和满足感等心理因素。
文化管理属于无为而治阶段,属于道的阶层。
如果一个企业精益生产一直处于低水平徘徊,甚至退化消弭,不是不努力,一定是这个企业的文化出了状况,或者是价值观和绩效文化产生导向偏转。
只要员工和企业文化高度契合,双方消除心灵上的障碍,激发人们能够产生“心流”的工作愉悦,才能实现个人的理想和价值。
这一层次主要由组织的一把手主导。目前社会上只有0.01%的企业能达到这个层次,算是万里挑一,目前算来算去还是只有丰田。
1989年以来,全球市值排名前十位的企业中半数来自于日本,但现如今,日本硕果仅存的只有丰田汽车一根独苗了,全世界最赚钱的车企依然是丰田,这一切都是偶然吗?
精益生产手法、脑法难吗,难的是心法,可见“改心“之难。
制造业精益转型升级不可能一蹴而就,耗费十年八年也很常见,但是必须要掌握精益生产的科学推进方法和路径。
有的企业刚开始开展的轰轰烈烈,随后偃旗息鼓;有的企业开展的磕磕绊绊,老是在生产环节小圈子使劲,收效甚微甚至倒退。
手、脑、心法的使用体现出一个人、一个组织做事的深度层次,精益生产、精益管理亦是如此。
文章分类
联系我们
联系人: | 阿道 |
---|---|
电话: | 17762006160 |
地址: | 青岛市黄岛区长江西路118号青铁广场18楼 |