敲黑板:为什么JIT很重要?
- 2021-07-20 10:00:00
- Jeffrey Liker
- 转贴:
- 微信公众号
- 637
《华尔街日报》最近的一篇文章引发了精益圈的热议,文章称汽车制造商正在从长达50年的准时制生产模式中退出。在过去的35年里,我听到过很多次这样的话了,就像每次丰田的供应链遭遇危机时一样。LEI曾多次质疑媒体过去针对JIT的错误言论,而这篇最新的文章甚至认为,这种明显荒谬的做法将很快消失。我想要重新审视和重申为什么准时制如此强大,并且会一直向前发展。
在这次疫情中出现了从纸巾、检测用品到疫苗等各种物资的短缺,而JIT也因为库存短缺原因得到了太多的赞扬和指责。我研究丰田(它经常被认为是JIT的原型)超过35年,我认为那些现在诋毁JIT的记者们其实并不了解JIT到底是什么,或者至少它是如何发展的,丰田是如何看待它的。
在许多攻击JIT的文章中,一个常见的误解是假定它主要是控制库存的策略。按照这种思路,库存越少越好,以便释放现金流,如果库存来自一个供应商,就会频繁地要求小批量的JIT交货,会让供应商持有库存,如果供应商导致了客户停线,需要为此付出高昂的代价。
这种狭义的、事务性的解释忽略了一个基本观点:丰田并没有把JIT看作是一个独立的政策或计划,而是把它作为丰田生产系统的一个组成部分。丰田将其核心供应商视为合作伙伴。正如大野耐一所说: “ 总公司通过压迫供应商来实现经营业绩,这完全不符合丰田生产体系的精神。”
库存的真正作用是作为使价值流向客户的缓冲。任何制造商直接接收用于生产的材料。这些材料的订单传统上是根据预测需求来安排的,这常常导致订单和需求之间的不匹配。
丰田选择通过使用来自生产线的拉动信号(即看板)来安排这些入站交付。需要这些材料的流程查看实际情况,并根据规则,在需要时订购库存以补充。一个简单的二进制信号——我需要更多,或我并不需要——将下订单的责任交给了了解自己处境的团队成员。
拉式系统的操作方式与排产类似。至少,必须订购足够的材料来覆盖补货时间。例如,如果你每周到货一次,你必须至少有一个星期的零件在手边,以覆盖这个交货期。如果零件是从海外运来的,需要4周的时间,那么你至少需要4周的库存。
这个库存作为补货所需时间的缓冲的做法,只有在一切都按照计划进行时才有效。但实际情况并非如此。变化总是存在的——这是我们最近经常看到的一个因素。
当货物的生产和运输出现问题时,我们需要一些额外的库存来应对可能发生的情况。这种紧急供应被称为安全库存。如果您在每周交付中所经历的最长时间有时是从您下订单的时间开始后的14天,那么您可能想要持有14天的库存——7天平均补货周期加上7天安全库存。
正确的JIT还考虑了客户需求引起的变化。如果客户需求突然从平均速率翻倍,您将需要最初的7天库存,加上7天的最大需求库存,再加上7天的安全库存,总共是21天的库存。
最重要的是,你总是面临着设备故障的可能性,或者你会因为供应商的材料短缺而停产。您必须增加足够的缓冲来应对这些意外事件。
希望大家能看得越来越清楚:准时制离零库存还很远。此外,带看板的拉式系统也不能避免前置时间和时间变化。从更详细的角度来看,应该会发现变异是JIT的敌人。
一、JIT的起源
当丰田汽车公司于1933年成立时,丰田喜一郎是从零起步。和许多初创公司一样,他们没有足够的现金来投资公司。他们没有供应商,他们甚至没有顾客。即使他们开始生产并得到了一些客户,他们仍然没有足够的现金来运营公司。
丰田面临的压力是快速生产产品并快速收到回款,这样丰田才能支付员工的工资和供应商的货款。丰田不能把钱都浪费在库存上,需要尽可能短的交货时间,使准时制成为必要。
正如大野耐一后来所说:“ 我们所做的就是紧紧盯着时间线,从顾客下订单的那一刻直到我们收到货款的那一刻。我们要不断缩短这一时间线。”
丰田喜一郎发明了准时制的理念,他非常注重细节,用一个4英寸长的活页簿,详细地描述了系统应该如何运行。它是看板系统的基础。看板不是天堂,而是一种妥协。
在理想的情况下,产品将沿着装配线流动,或每次单件产品通过一个单元,没有库存。但这对于像冲压这样的批处理或来自远方供应商的零件来说是不太现实的。所以当需要存货时,用看板来控制。
这一切都很好,但是看板并没有解决问题的根本原因。正如我们在安全库存中看到的,顺畅流动的障碍是各种形式的变异。这可能是客户需求的变化、生产线速度的变化、由人执行的手工任务的变化、设备功能的变化、交付流量的变化、供应商内部流程的变化等等。
当然,没有一家公司,包括丰田,可以控制一切,所以变异是不可避免的。但是丰田家族的一个特点是坚韧不拔。他们会工作、试验、努力控制他们所能控制的一切,以使价值流稳定。
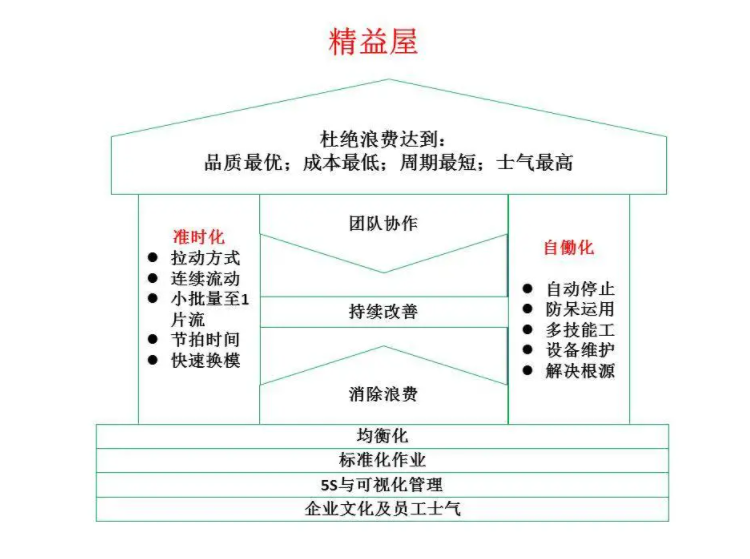
这导致了著名的安灯系统,机器或工人实时识别问题并停止进程。其目的不是继续关闭生产,而是识别和纠正发生的偏离标准条件的情况。有成千上万的过程,谁能做到这一点?答案是团队成员和他们的班组长以及团队领导——那些对过程负责的人。因此,每个人都必须成为问题解决者。
仅仅停下来解决问题是不够的。如果丰田组装厂就像坐过山车,追逐变化的客户需求,就会有太多的变化需要控制,而众所周知的“牛鞭”效应会对供应商和供应商的供应商造成更大的破坏。你越往回看,你就会发现丰田的节拍或客户需求的速度变化越具有破坏性。
唯一的解决方案是,当你在供应链上向后移动时,保持越来越多的库存。因此,为了表示对供应商的尊重,使作业的流动保持平稳,丰田引入了均衡生产,即生产平顺化。
均衡生产被描述为TPS的基础,意味着丰田不会按照客户需求的顺序来生产产品,而是收集一段时间的需求,然后将其平顺化。这会产生一个稳定的节拍,并为整个生产过程创建一个目标-构建到客户需求的平均值。
当然,丰田不可能满足客户需求的所有变化,所以他们开发了一个灵活的、自适应的系统。这包括在同一条装配线上生产多种产品,这样一来,虽然对某一种车型的需求可能会上升或下降,但各车型的平均需求将更加稳定。
它还包括拥有一个灵活的劳动力队伍,可以根据需要增加或减少工作时间。例如,通过两班倒而不是24小时工作,班次之间有时间来增加或减少加班。
就这样,整个丰田生产体系得以发展,丰田的学习也得以发展。例如,大野耐一后来发现JIT的好处不仅仅是减少库存和更快地获得回款。在他著名的降低水位让石头显露出来的类比中,他发现过多的库存消除了改善过程的压力。
毕竟,如果你的供应商或之前的流程中断了,只要你有库存,你可以继续工作。另一方面,如果供应中断威胁到立即关闭装配线,你将感到巨大的压力,保持生产线运行,并解决出现的问题的根本原因。
这就是一个几乎没有库存的连接过程系统会鼓励甚至需要持续改进。事实上,JIT是一种暴露问题并支持持续改进的方法,持续改进让流程更加稳定,并支持了JIT。
我最近的第二版《丰田模式》将JIT定义为:
“一种连续流动的系统,它将小批量的所有材料和信息带到需要使用的地方——既不太早也不太晚。”这就避免了包括过量生产在内的浪费,并创造了一个更高效的流程,快速发现异常,这样人们就可以提高质量、成本、准时交付以及对客户需求变化的响应能力。”
二、JIT不是所有危机的答案,也不是原因
尽管丰田已经对准时制的力量进行了数十年的实践和学习,但它今天仍然无法避免严重的零部件短缺问题。就像你不能从岩石中榨出水一样,没有零部件,丰田也无法制造汽车。而当丰田没有预料到需求突然激增时,它也无法满足需求。
在新冠肺炎爆发初期,卫生纸等物资被抢购,这给每个人都带来了问题。如果由于自然灾害或供应商工厂或运输系统的故障,关键部件停止流入丰田工厂,丰田确实会很快用完部件,如果是JIT供应商,且系统中库存很少,则会更快消耗完零件。有一个简单的解决办法——所有零件保留6个月的库存,成为仓储企业而不是制造商。
丰田有意识地选择不奉行这一政策。这样做会抹杀我所描述的JIT的所有好处。相反,可以考虑这样的对策:在正常情况下保持必要的库存以满足生产和交付时间,同时持有足够的安全性和缓冲库存以满足可变性。
在这种情况下,库存策略将随每个零件而变化。丰田通过PFEP(对每个部件做计划)来做到这一点。这就是为什么工厂位于丰田工厂附近的高度可靠的供应商要求最低数量的库存,而海外供应商或流程不受控制的供应商要求更多的库存。
如果有一场预测中的灾难,比如即将到来的海啸,就需要更多的库存。丰田在世界上的每个地区都有两到三个货源,并试图让一个地区的发货点在地理上分散,以此对冲风险。
事实上,就连《华尔街日报》的那篇文章也奇怪地承认,丰田本身(JIT的代名词)也能成功应对极端情况。后一种多家分散供应商的做法是丰田多次吸取的教训。例如,2011年导致核电站熔毁的福岛地震导致日本中部地区的供应商关闭。
其中一家被关闭的供应商是一家为多个客户服务的计算机芯片供应商。这是丰田提供这些零部件的唯一来源,所以当一家工厂倒闭,全球停产数月时,丰田没有芯片可用。这不是JIT的失败,事实上这不是一个JIT供应商。
这是丰田遵循自己的供应商战略的失败。经验教训:拥有多个地理上分散的生产来源,当一个生产来源面临风险时,保持库存。他们做了这两件事,包括要求供应商保留数周的芯片库存,因此这种做法在2021年芯片短缺导致许多竞争对手关闭的情况下让公司大大受益。
即使丰田没有改进它的准时制方法,并在周期性短缺的情况下面临长达数月的停工,它也绝不会在TPS的背景下放弃准时制。追求无浪费的单件流是丰田经营理念的核心。这种哲学不会随着危机而改变。相反,丰田应对危机的方式是进行深刻反思,思考需要学习和调整的地方。
当出现危机时,丰田还受益于其与一级供应商的紧密合作关系,他们聚集在一起,尽快解决问题。这在1997年著名的神户地震中很明显,当时所有刹车系统所需的P型阀的唯一供应商停产了。
只有2-3天的库存可用,全面的停产似乎迫在眉睫。然而,200多家供应商自发组织起来,开发生产P型阀的能力,并在几天内为丰田供货,从而避免了灾难。
三、丰田集团以外的公司能通过JIT做什么?
不幸的是,促使《华尔街日报》发表这篇文章的一个合理原因是,许多公司都采用了准时交货作为减少库存的政策,而没有使用丰田的任何支持系统。仅仅将其作为一个工具单独实现可能会导致许多问题。
请记住,JIT的一个好处是,问题可以很快浮出水面,从而可以得到解决。对于一个在整个价值链中没有高度发展的人员和供应商的公司来说,让问题浮现是不可取的。
缺乏成熟的精益系统和没有充分发展其人员的公司只能从JIT中获得有限的好处,而使用像看板这样的工具可以帮助库存控制。但主要的敌人永远是管理变异的危险。而且,你拥有的变异越多,你需要的缓冲库存就越多。
最重要的是,丰田学会了在有可靠的零部件和材料供应的情况下,稳定生产流程,同时减少库存。他们已经表明,与成为合作伙伴的关键供应商合作将带来更高的可靠性和更少的库存。努力稳定自己的流程,让它以稳定的节拍连续流动,也将减少所需的库存数量。
而且,坚持不懈地解决生产进度平稳性(或平顺性)这一难题,将会带来巨大的好处,特别是当一个人在各个层级的供应商之间进行协调时。这并不是说丰田的解决方案可以被复制。
每个公司都处于独特的情况下,需要努力发现自己的方法,朝着纯粹的价值流的方向前进,以提供客户想要的东西,以他们想要的数量,在他们想要的时候。
这一切都需要时间和大量的努力。丰田已经完成了这项工作,并享受了这些好处。该公司明白,当他们预计即将出现危机或没有可靠的材料来源时,有必要保持库存。
然而,这些都是需要背离更广泛实践的偶发事件。更重要的是理解JIT的目的以及它在更深层次系统中的位置。公司和记者们不应该勉为其难,在JIT不可能的时候假装它可能,或者在JIT可能的时候假装它不可能。相反,他们应该专注于朝着精益供应系统的方向努力,以享受它带来的强大利益。
文章分类
联系我们
联系人: | 阿道 |
---|---|
电话: | 17762006160 |
地址: | 青岛市黄岛区长江西路118号青铁广场18楼 |